Natural pure cotton fiber fabric has outstanding characteristics, such as air permeability, moisture absorption, softness and comfort, due to the fact that its molecular structure contains more hydrophilic groups and low crystallinity. In addition, it has many advantages such as low cost, friendly price and degradability. It has a broad market, considerable sales volume and is deeply loved. The non ironing finishing can not only effectively improve the elasticity and wrinkle resistance of cotton fabric and maintain the stability of the original size, but also weaken or even avoid the deformation and wrinkle of fabric fiber due to external force, or the relative displacement between the basic units of its structure, the fracture of hydrogen bond and the re formation of hydrogen bond, so as to achieve the effect of wrinkle prevention, washing and wearing. The specific method is to add finishing agent to crosslink the hydrogen bond between it and the fiber to form a permanent and irreversible three-dimensional network structure. This technology has become an important field of fabric finishing and has a very broad market prospect.
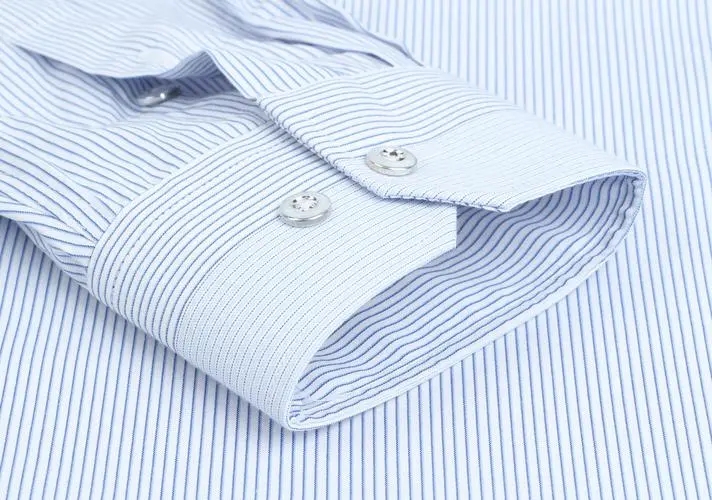
As early as 1929, the first anti wrinkle finishing patent was successfully applied for. However, at that time, this process did not attract the due attention of the majority of scientific and technological workers. In production practice, it was not popularized and used, and stopped in the laboratory. This situation lasted for nearly 40 years. It was not until the 1960s that the development of fabric non ironing finishing technology really kicked off. With the rapid change of the chemical industry, a variety of fine chemical products continue to push through the old and bring forth the new, which objectively and effectively promoted the development of non ironing finishing technology. So far, it has a history of nearly 100 years.
In 1918, urea formaldehyde resin (UF for short) was first reported. The British John mixed urea with formaldehyde and reacted under certain conditions to make thermosetting resin, namely urea formaldehyde [23]. This is the earliest finishing agent. Using it to treat clothes can reduce the formation of wrinkles and reduce the shrinkage of fabrics. It is commonly known as resin finishing. Subsequently, in the late 1930s, the large-scale industrialization of melamine made a series of derivatives widely used. For example, melamine formaldehyde (MF) primary shrinkage partially replaced urea formaldehyde resin and occupied part of the market. In 1947, the appearance of dimethylol ethylene urea (DMEU) further improved the finishing effect. Not only the stability of Anti Wrinkle finishing dip rolling solution was significantly strengthened, but also after adding it for finishing treatment, the wrinkle resistance and washing resistance of the fabric were greatly improved, the market share changed, and the urea formaldehyde resin was further reduced. It is precisely because of its emergence that the crease resistant finishing of cotton fabric has ushered in a rapid development.